Alcast Company for Beginners
Alcast Company for Beginners
Blog Article
Alcast Company Can Be Fun For Everyone
Table of ContentsGetting My Alcast Company To WorkAlcast Company for DummiesAlcast Company Things To Know Before You BuyAlcast Company for BeginnersAlcast Company - The FactsMore About Alcast Company
The subtle difference hinges on the chemical web content. Chemical Comparison of Cast Light weight aluminum Alloys Silicon advertises castability by lowering the alloy's melting temperature level and boosting fluidity throughout casting. It plays an essential duty in allowing intricate mold and mildews to be loaded precisely. In addition, silicon adds to the alloy's stamina and wear resistance, making it important in applications where sturdiness is crucial, such as automotive parts and engine components.It also improves the machinability of the alloy, making it simpler to refine right into finished products. In this way, iron contributes to the general workability of light weight aluminum alloys.
Manganese adds to the strength of aluminum alloys and boosts workability (aluminum metal casting). It is generally made use of in wrought light weight aluminum items like sheets, extrusions, and profiles. The visibility of manganese help in the alloy's formability and resistance to splitting during manufacture processes. Magnesium is a light-weight component that provides strength and effect resistance to light weight aluminum alloys.
Rumored Buzz on Alcast Company
It enables the production of lightweight components with outstanding mechanical residential or commercial properties. Zinc boosts the castability of light weight aluminum alloys and helps control the solidification process during casting. It boosts the alloy's stamina and solidity. It is usually located in applications where intricate forms and great information are required, such as decorative spreadings and specific vehicle parts.
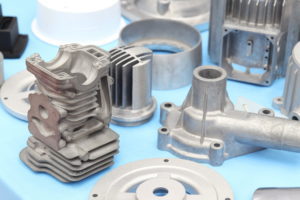
The key thermal conductivity, tensile strength, return toughness, and prolongation differ. Among the above alloys, A356 has the greatest thermal conductivity, and A380 and ADC12 have the most affordable.
The smart Trick of Alcast Company That Nobody is Talking About
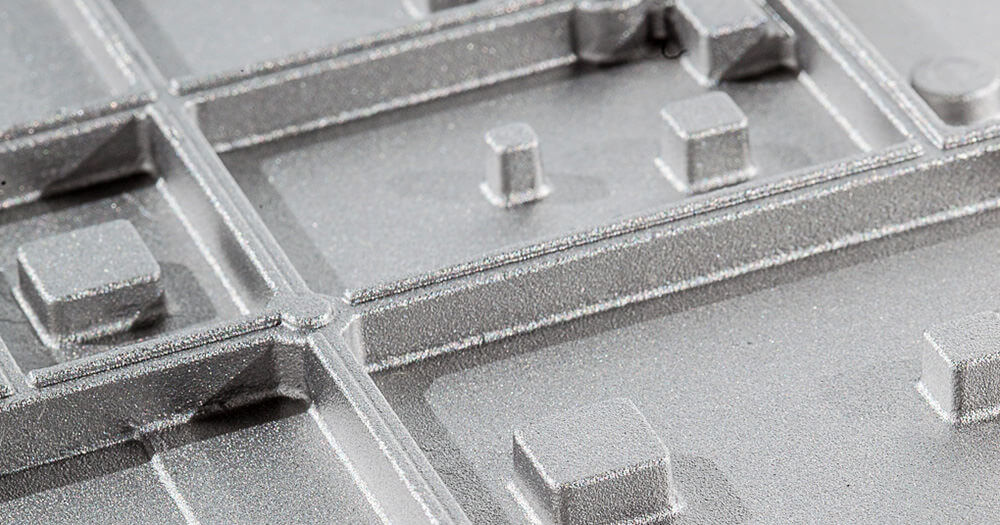
In precision spreading, 6063 is well-suited for applications where complex geometries and high-grade surface coatings are paramount. Instances include telecommunication enclosures, where the alloy's remarkable formability enables smooth and visually pleasing layouts while maintaining structural integrity. Likewise, in the Illumination Solutions industry, precision-cast 6063 parts develop sophisticated and effective illumination fixtures that need complex forms and excellent thermal performance.
The A360 shows remarkable prolongation, making it ideal for complicated and thin-walled parts. In precision spreading applications, A360 is appropriate for industries such as Customer Electronic Devices, Telecommunication, and Power Devices.
An Unbiased View of Alcast Company
Its distinct properties make A360 an important option for precision casting in these markets, boosting product resilience and quality. Aluminum Castings. Aluminum alloy 380, or A380, is an extensively utilized spreading alloy with a number of distinctive characteristics.
In accuracy casting, light weight aluminum 413 radiates in the Consumer Electronic Devices and Power Equipment industries. It's typically utilized to craft complex parts like smart device real estates, electronic camera bodies, and power tool coverings. Its precision is exceptional, with tight resistances approximately 0.01 mm, guaranteeing flawless item assembly. This alloy's premium corrosion resistance makes it an outstanding option for exterior applications, ensuring lasting, resilient products in the stated industries.
Get This Report on Alcast Company
The light weight aluminum alloy advice you select will considerably impact both the casting process and the buildings of the final item. Due to the fact that of this, you need to make your choice thoroughly and take an educated technique.
Establishing the most appropriate light weight aluminum alloy for your application will certainly indicate weighing a broad variety of characteristics. The first group addresses alloy qualities that affect the production procedure.
The Single Strategy To Use For Alcast Company
The alloy you choose for die spreading directly affects a number of aspects of the spreading procedure, like exactly how very easy the alloy is to deal with and if it is prone to casting flaws. Warm fracturing, additionally known as solidification cracking, is a typical die spreading problem for aluminum alloys that can cause interior or surface-level splits or cracks.
Specific light weight aluminum alloys are a lot more susceptible to warm breaking than others, and your option should consider this. It can damage both the cast and the die, so you ought to look for alloys with high anti-soldering residential properties.
Rust resistance, which is already a noteworthy quality of aluminum, can differ considerably from alloy to alloy and is a crucial characteristic to consider depending upon the ecological problems your product will be revealed to (aluminum casting manufacturer). Put on resistance is an additional residential or commercial property typically looked for in light weight aluminum items and can set apart some alloys
Report this page